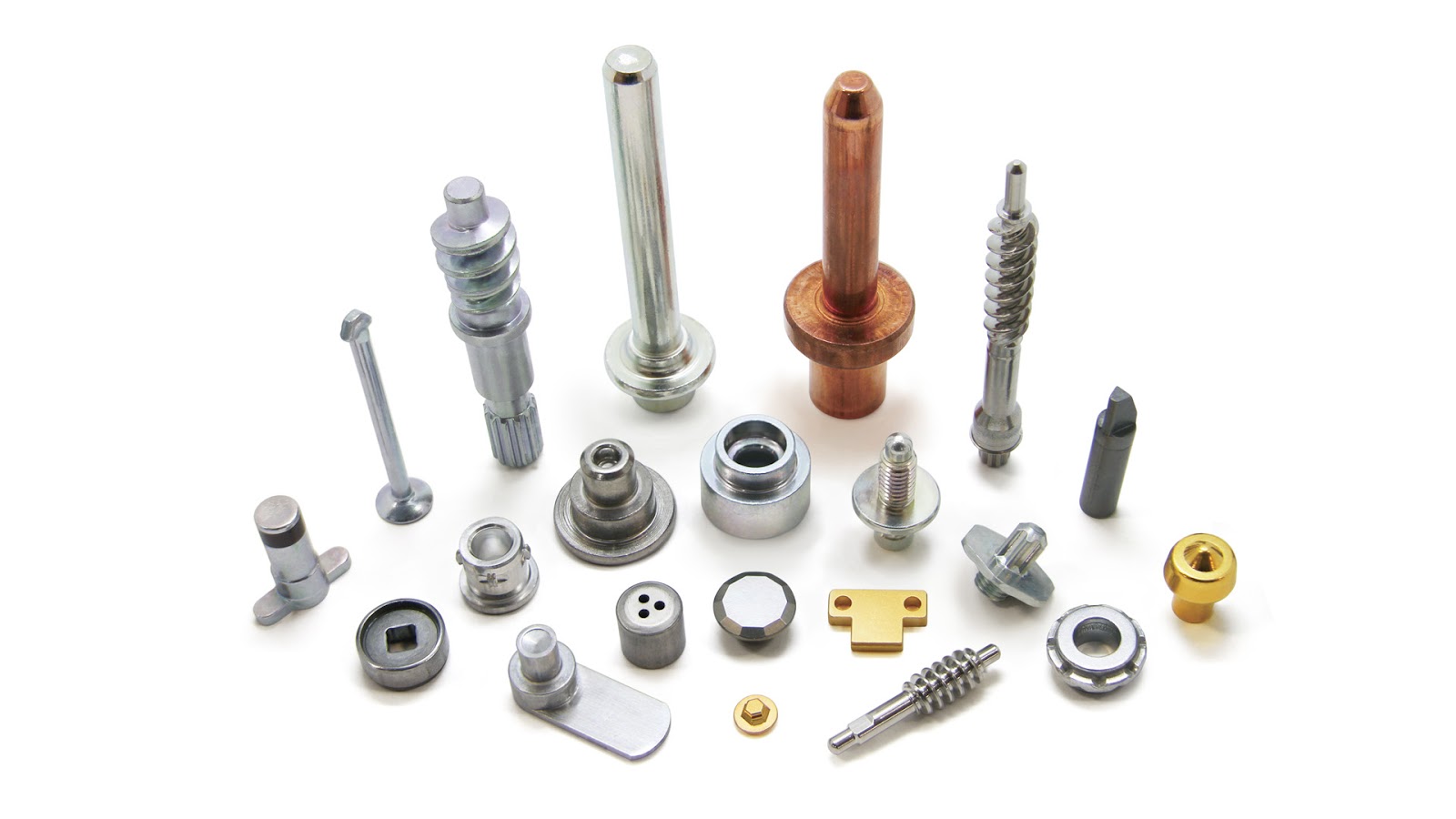
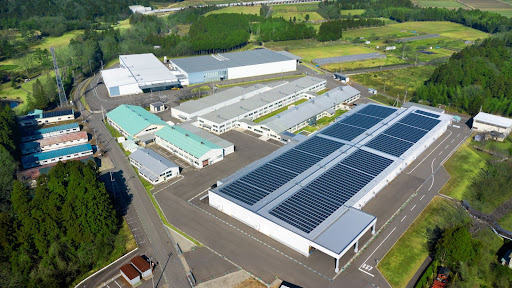
本社所在地 福井県あわら市山十楽1-7
代表者 代表取締役 打本 幸雄
創 業 1959年11月3日
資本金 4億5千万円
従業員数 569名
事業内容 特殊形状の精密鍛造パーツ及びファスニング製品と省力機器の製造・販売
事 業 所(生産拠点) 細呂木事業所・加賀工場・能登工場・NL工場
事 業 所(営業拠点) 営業部・東京支店・大阪支店・名古屋支店・国際ディビジョン
認証取得 IATF 16949, ISO 9001, ISO 13485 , ISO 14001製造許可 医療機器製造業許可(許可番号:18BZ200052)
目次
introduction
鋲螺(びょうら)とはネジクギのこと。福井鋲螺株式会社(福井県)の第一歩は、60年前のリベットの製造でした。「冷間鍛造技術」は、省エネルギーで、金属材料の廃棄物はほぼゼロという、環境に優しいすぐれもの。この技術を駆使して生まれるメタルパーツは、世界にも歓迎されています。
今回は、同社の花山昭弘さん、杉本秀俊さんに、メタルパーツの様々なお話をSDGsの視点をまじえてご紹介いただきました。
ネジバナはものづくりへの情熱のシンボル
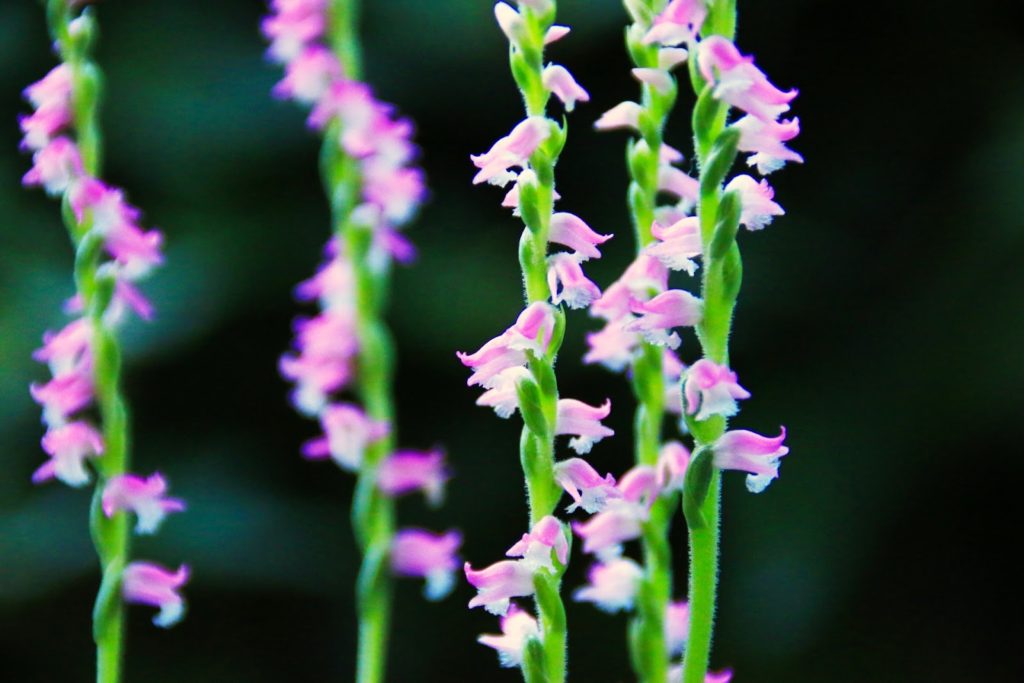
–まずは、社名にもある「鋲螺」について教えてください。
花山さん:
鋲螺は「びょうら」と読み、「鋲」は画鋲の鋲、リベットやクギを表す漢字です。「螺」は螺旋階段の螺、つまりはネジです。あわせた「鋲螺」はネジクギを意味します。ネジクギを製造する会社はたくさん存在していて、その多くが「鋲螺」を社名につけていますね。弊社は、福井県にありますから「福井鋲螺」と名づけられました。
社名ロゴの「鋲」のノの部分がピンク色ですが、これはネジバナがモチーフです。ネジのようにピンク色の花が並んで咲く、弊社のシンボルのような花です。
–鋲螺のちょっといかめしい文字が愛らしくなりますね!企業理念にもネジバナ愛は反映されているのでしょうか?
杉本さん:
基本理念は、「より良き品を創意と熱と人の和で」です。「快適な暮らしを支える企業」「環境にやさしいものづくりを実践する企業」として、社会に貢献しながら発展し続けることを目指しています。
弊社のロゴマークは、グレーとピンクの花びらが繋がり合ったようなマークですが、ピンクは社員の「創造力と情熱」、グレーは「技術力と品質」を表しています。このマークの形はネジバナが成長する時に形成する「螺旋」から、無限に上昇し続ける(成長を続ける)企業イメージと、福井鋲螺のルーツである「螺子」のイメージを重ねています。企業理念がこめられたデザインです。
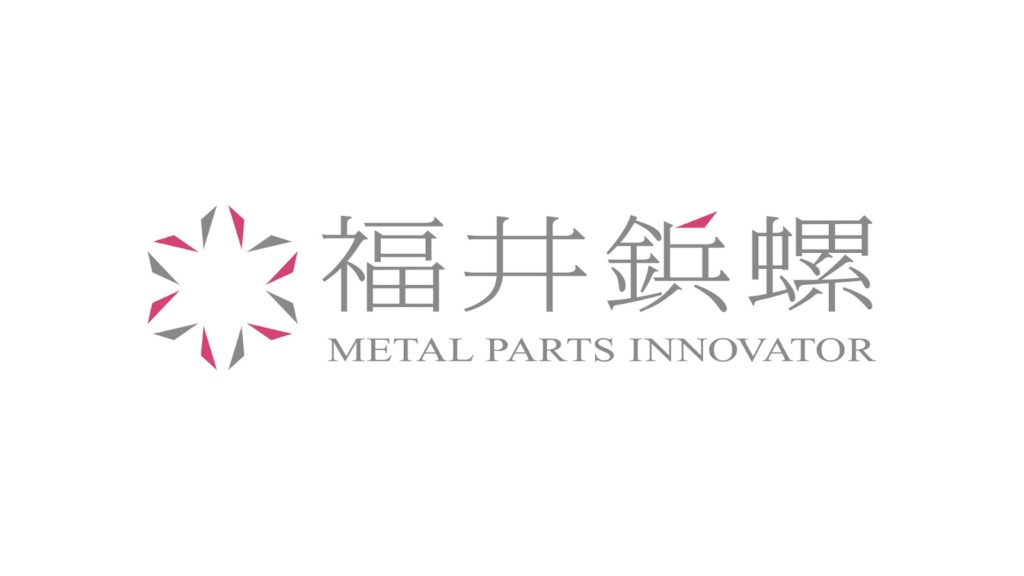
CO₂排出も、廃棄物も少ないエコな「冷間鍛造技術」
–環境への優しさも伴いつつ、鋲螺から発展してきた業務内容をご紹介ください。
花山さん:
「福井鋲螺」の社名ロゴの下には、METAL PARTS INNOVATORというサブタイトルがあります。「金属部品の革新者」という意味ですが、その名のとおりに、金属部品の改革、革新が弊社のポリシーです。
現在は精密部品の引き合いが多く、様々なメタルパーツを製造しています。創業の1959年以来、品質の良さを評価していただき、自動車、家電、通信機器、医療、建築、ファッション、アミューズメント業界に至るまで、多種多様な業界と取引があります。
メタルパーツといっても、アルカリ電池のなかにある極小のピン状のものから、1m以上のものまで、大きさも種類も様々です。蛍光灯の両端に、プラグのような形の端子がありますよね。あれは、ほぼ弊社の製品なんです。難しい技術が要求されるパーツで、世界市場での弊社のシェアは60%、国内では80%を占めています。
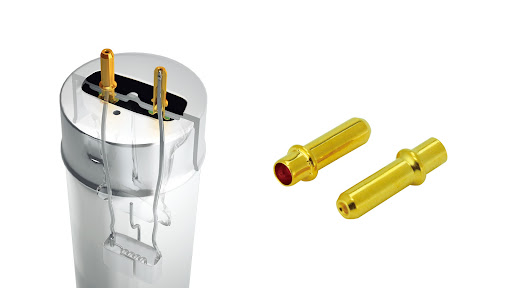
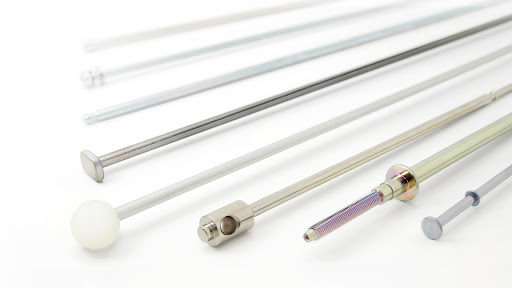
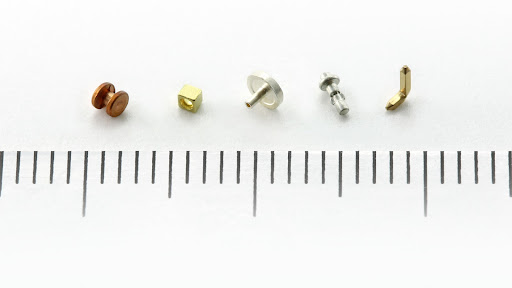
弊社の製品のもっとも大きな特色は、「冷間鍛造技術」という加工方法で作られている点です。省エネルギーで、資材で廃棄する部分がほぼないという、環境にやさしい技術です。創業当初から採用していますが、今、まさにSDGsの方向性にかなっていると自負しています。
–金属の鍛造は高温によるというイメージがありますが、御社は「冷間」なんですね。環境にもやさしいとのこと、ぜひ詳しく教えてください。
花山さん:
鍛造には、①1000℃以上で金属がどろどろに溶ける直前まで熱して変形させる「熱間鍛造」、②300℃くらいで変形させる「温間鍛造」、③200℃以下の「冷間鍛造」、の3通りがあります。「冷間鍛造」は、鍛造時に熱は加えません。ですから、「冷間」といっても冷たいわけではなく、常温なんです。
加工方法は、材料のワイヤーを一定の長さにカットし、それを金型に入れ、圧力を加えて形を変えていきます。もちろん、高温のほうがたやすく変形させられます。「鋳造」などは、どろどろに溶かした金属を鋳型に流し混んで成型しますから、より容易ですね。
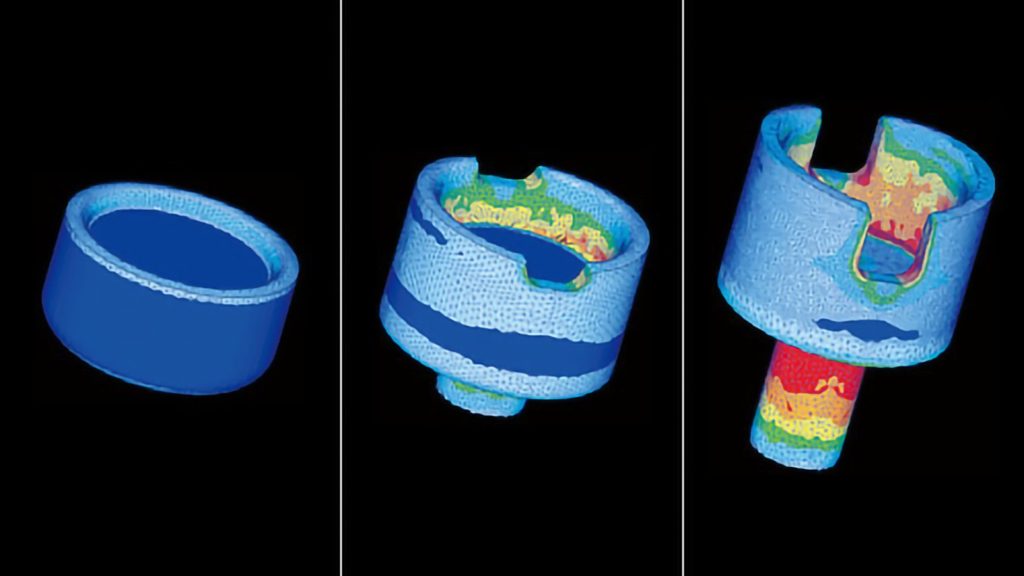
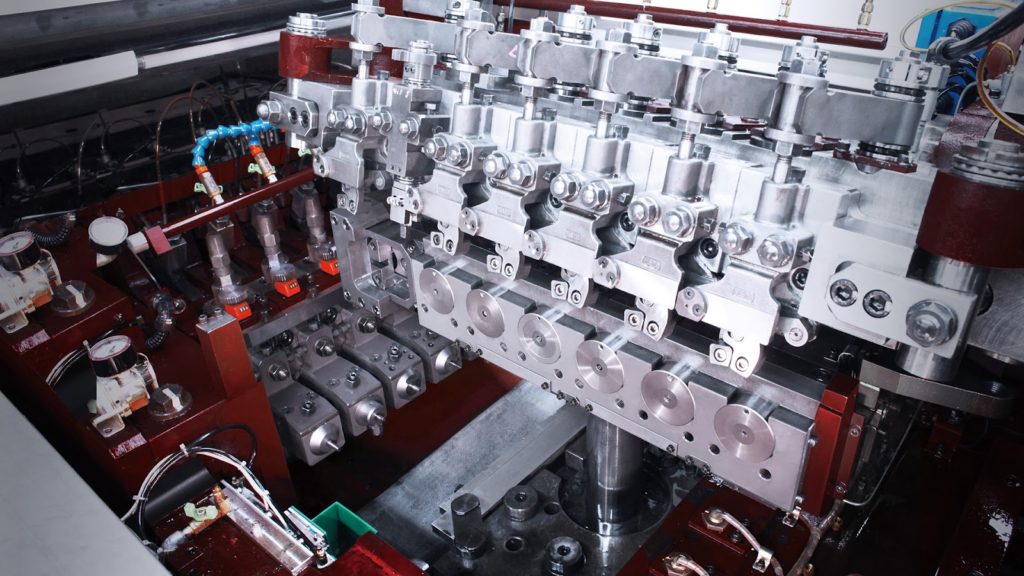
「冷間鍛造」は、熱を加えないぶん、大きな圧力をかける加工となりますから、製品にひずみや亀裂が生じやすいんです。それを、当社は技術革新で克服していきました。金属は熱を加えると膨張・収縮がありますが、「冷間」では金属の熱変形がないため、ばらつきが少なく、高品質な製品を作れます。
「冷間鍛造」は、SDGs的にも、とてもすぐれものなんです。熱源が必要ありませんから、電気を使うのは動力に関してのみ。つまり、CO₂の排出量は圧倒的に少ないです。また、材料を変形させて作りますから、削ってつくる「切削」のように、廃棄物が出ることもありません。資源を無駄にせず、ほぼ100%使いきれるんです。
たとえば、切削加工していたあるパーツでは、一個あたり2.9gのスクラップが発生していましたが、100%冷間鍛造化したことによって、金属スクラップを年間9.9トンも削減できました。
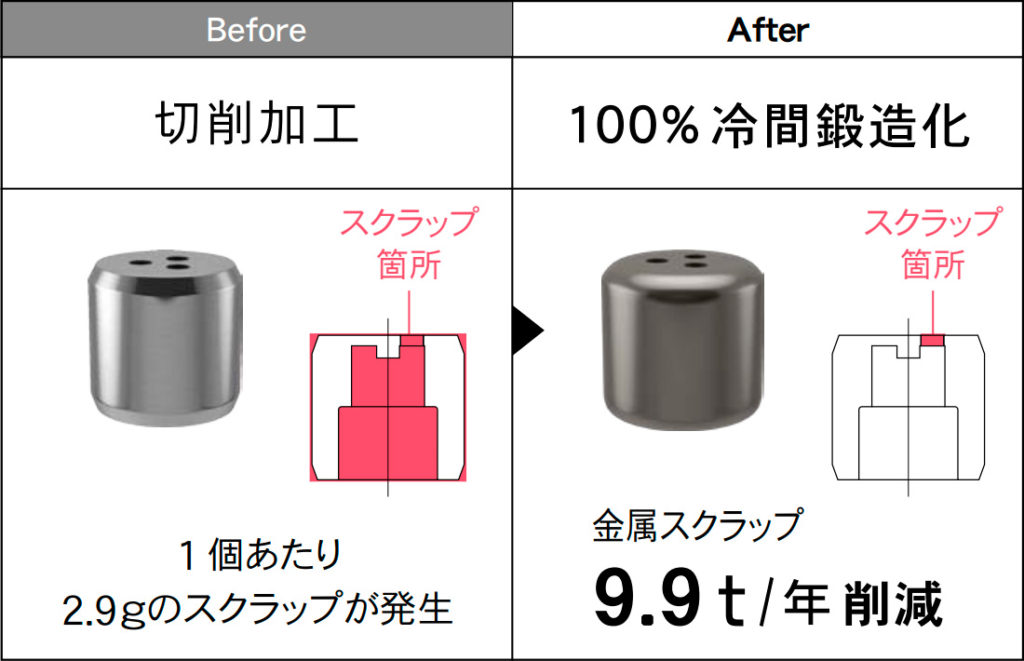
また、「プレス加工+冷間鍛造+その二つの部品を結合=3工程」だったものを、冷間鍛造1工程にすることで、プレス打ち抜き時のスクラップを年間10.1トン分削減することにも成功しました。1工程化により、省エネルギーとなり、CO₂も削減できています。

環境に優しく価格も抑えられる高品質パーツ
–加熱用の電力が必要なく、あますことなく材料を使えるのですから、低コストですね。エコなものは価格が高めになりがちですが、御社の製品は逆に安価ということですか?
花山さん:
その通りです。蛍光灯の端子が、国内外で圧倒的なシェアを持っているのも、高品質かつ価格競争にも勝てるからです。
実際に廃棄物が出る工法のものを他社から購入されているお客様に、弊社の製品は廃棄物が出ないぶん材料購入費が安く、CO₂排出も少ないことをご説明し、かつ価格のリーズナブルさをお伝えすると、弊社にパーツ製作を依頼されることが多いですね。
弊社製品への切り替えが進むほどに、CO₂も廃棄物もそのぶん世の中から減るわけですから、それも大きな環境への貢献だと考えています。おかげさまで、資源エネルギー庁が定める改正省エネ法の事業者クラス分け評価制度で、7年連続で最高ランクのSクラス認定を受けています。
冷間鍛造の技術は、日本の工業界に行きわたってはいるのですが、弊社は生産設備も金型も社内で作れるんです。通常の汎用機では製造できないような形状も生産設備の開発からおこなえますので、その技術力の結果、環境への成果も大きなものとなっています。
–創業以来の製造方法が、おのずからエコだったんですね。SDGsを意識し始めたのはいつごろからですか?
花山さん:
もともと、環境に優しいものづくりを自負していた弊社ですから、SDGsが叫ばれだした際、自分たちの取り組みがSDGsに関連していると気づきました。社長からのトップダウンで、17のゴールに併せて仕事を見直すなどしてきましたが、2021年には、SDGs事務局が6名体制でスタートしました。
会社周辺の清掃活動なども実施していますが、社長や役員も参加し、経営陣のリーダーシップと本気度を見せてくれています。
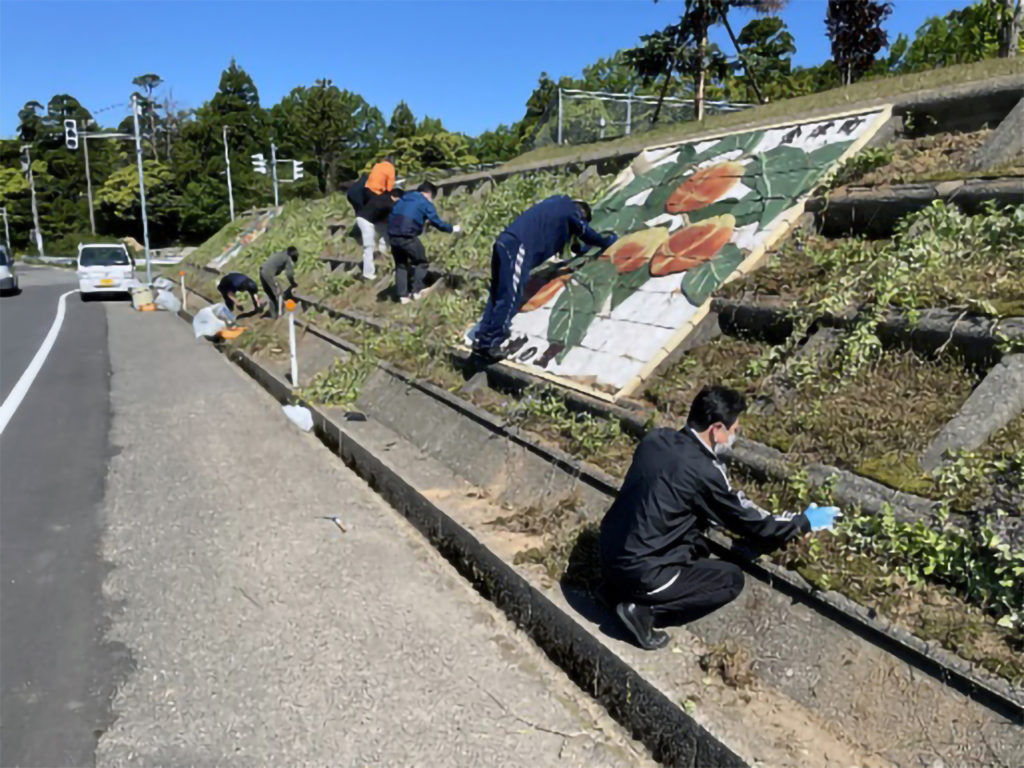
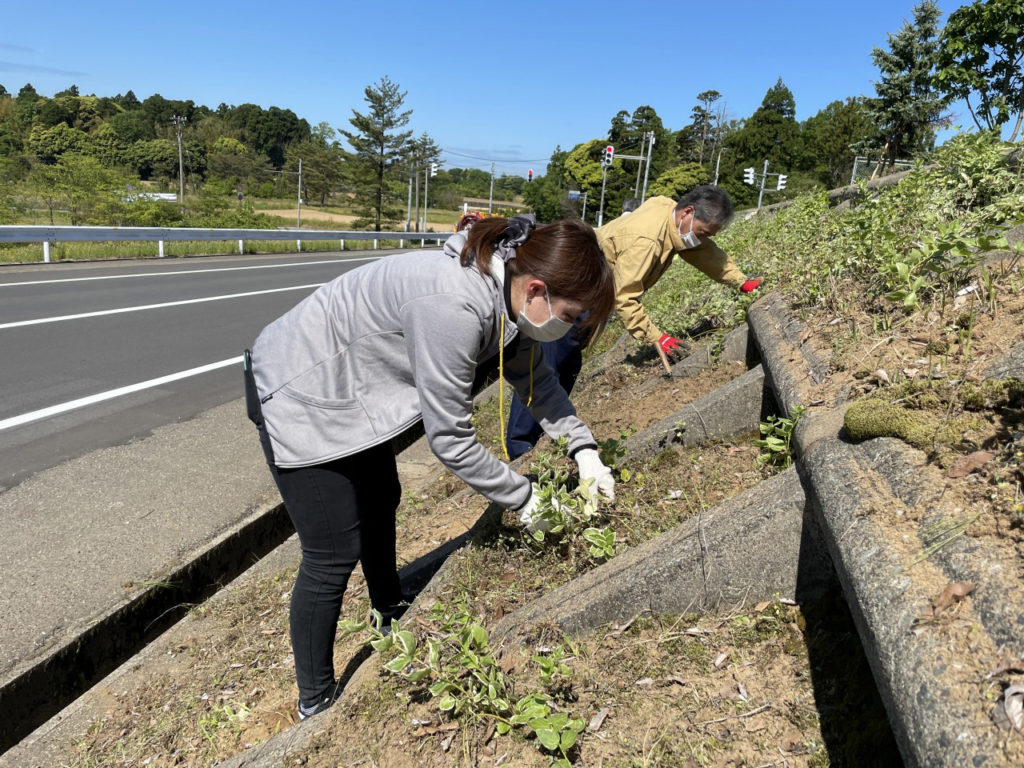
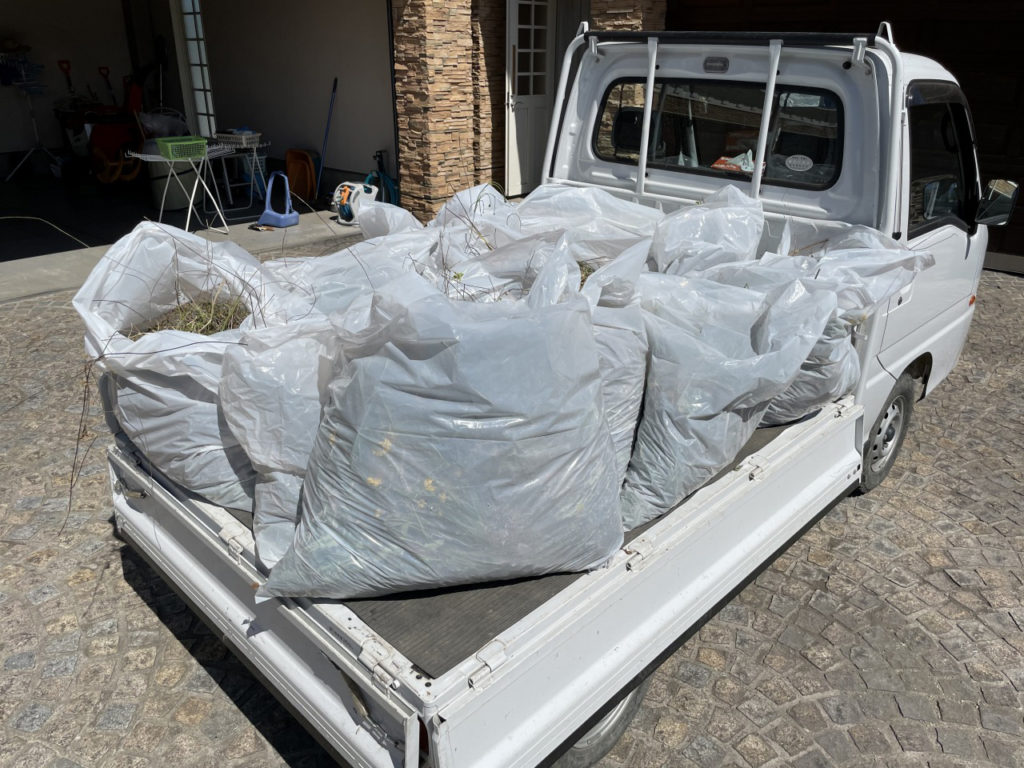
北陸最大級の太陽光発電設備を導入し、さらなる環境貢献をめざす
–製造以外でのSDGsへの取り組みをお聞かせください。
杉本さん:
2021年3月、細呂木事業所(福井県あわら市)で、自家消費型としては北陸最大級の太陽光発電設備の運用を開始しました。北陸電力ビズ・エナジーソリューション(株)との契約によるものですが、2022年2月からは、加賀工場(石川県加賀市)でも同様の設備が稼働しています。
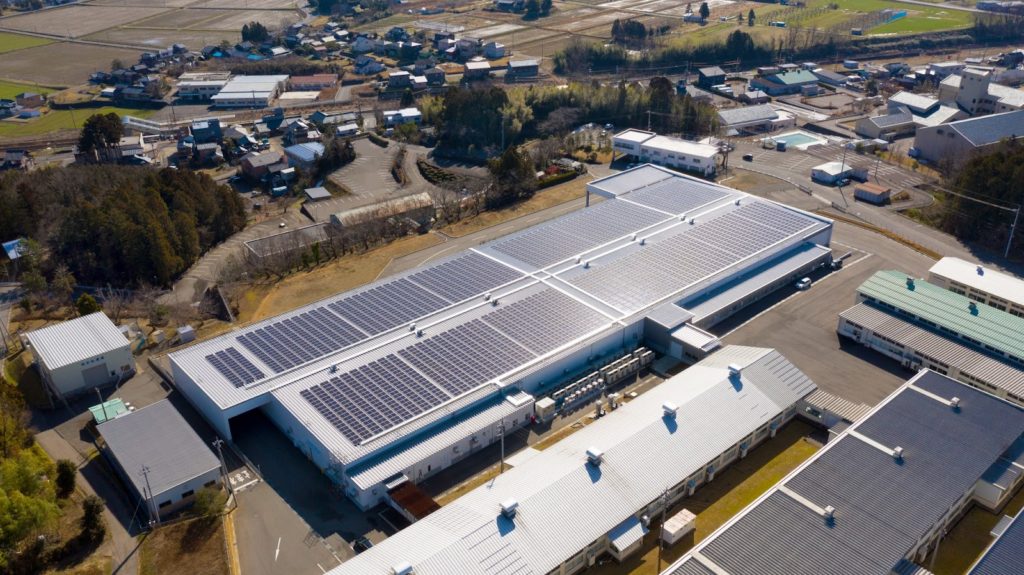
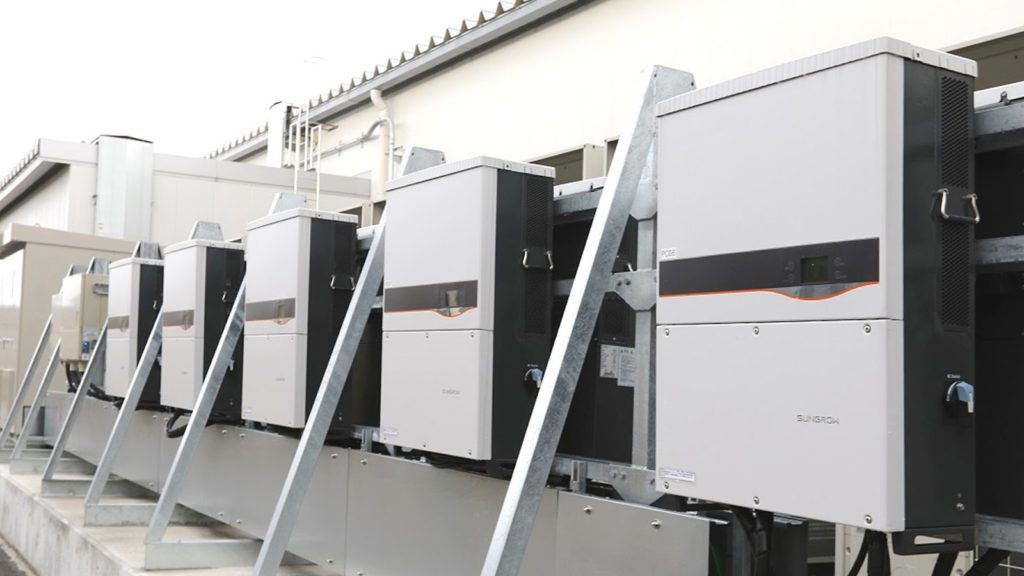
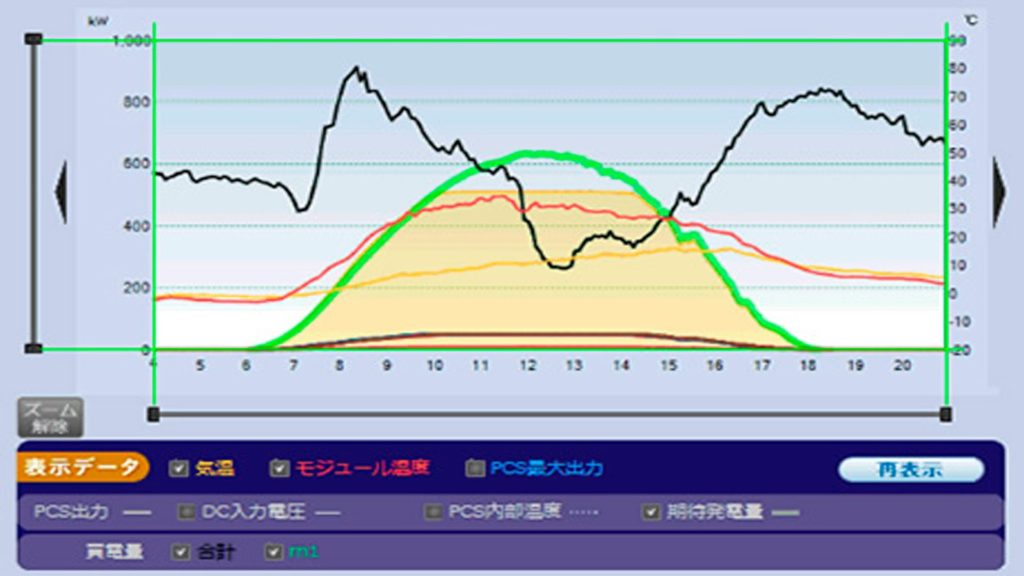
両設備ともに、それぞれの施設のエネルギーの1割を担っています。とくに細呂木事業所では、太陽光発電で製造しているのが、電気自動車のバッテリー部品なんです。環境に優しい電力を使って、環境に優しい加工方法で、環境に優しい車のバッテリー部品を作っているという、嬉しい状況ですね。
この設備を使って、今後のCO₂排出量の削減目標を立てていて、第一段階としては、2013年に排出したCO₂量をターゲットに、2025年までにその量のCO₂排出削減を目標に取り組んでいます。第二段階として、2030年までにカーボンニュートラルを目指しています。
花山さん:
弊社は、社員の労働環境も大切にしています。トイレにもエアコンをつけたりする分、機器は極力省エネのものに切り替えるなど、社員への快適な環境提供と省エネ導入のバランスを取っています。
コロナ禍でテレワークも進み、さらに2021年12月に福井市中心部にサテライトオフィスを作りました。その結果、社員のほぼ全員が車通勤の弊社としては、車のCO₂削減と、社員の働きやすさの両方を改善できました。子育て中の社員や、雪深い冬の出勤などに、フレックスタイムも大いに活用してもらっています。通常、製造担当者には適用が難しいフレックスタイムですが、弊社では可能です。
変わったところでは、近くの温泉旅館と提携し、会社の補助で社員とその家族が宿泊できる制度を作りました。心身のリラックスは大事ですから。
杉本さん:
対外面では、小・中・高・大の学校を対象に、工場見学を受け入れています。ものづくりへの関心をもってもらうことに併せ、SDGs教育の目的もあります。工場見学では、まず弊社の技術がなぜ環境に優しいのかをわかりやすく伝えるプレゼンをします。そのあと、実際に工場の生産現場を見てもらい、本当に廃棄物なしに製品が作れることなどを実感してもらうことが多いですね。
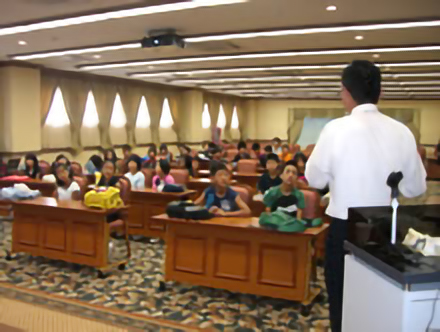
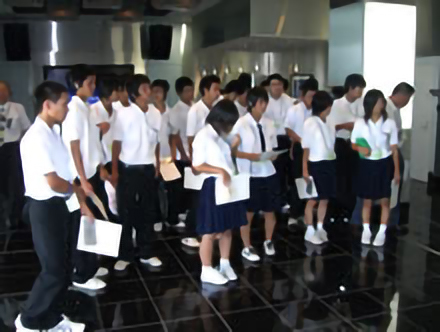
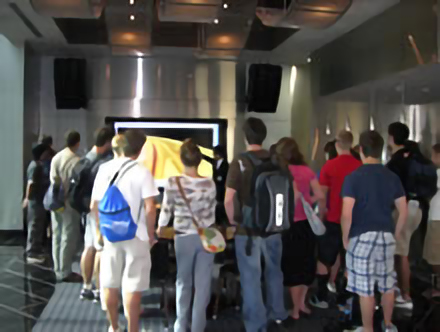
–最後に、今後への展望をお聞かせください。
花山さん:
冷間鍛造のコア技術をこの先もブラッシュアップしていく予定です。環境に優しい製品を作り続けることで、世界に貢献できると考えています。現在世界に納めている製品は多々ありますが、さらに拡大していきたいですし、地球規模で貢献できるような製品も開発したいですね。
–販売増加が、環境への貢献とイコールですね。今日はありがとうございました。
福井鋲螺株式会社:https://www.byora.co.jp/
この記事を書いた人
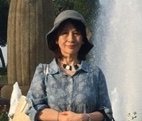
壱岐 梢 ライター
ライティング、詩作、翻訳…様々なかたちで言葉と共に仕事をしています。 この世界に入ったきっかけは、宮沢賢治との出会いでした。彼は究極のSDGs 実践者。大好きな言葉の仕事によって、今SDGsに取り組む皆様をご紹介 できることは、大きな喜びです。
ライティング、詩作、翻訳…様々なかたちで言葉と共に仕事をしています。 この世界に入ったきっかけは、宮沢賢治との出会いでした。彼は究極のSDGs 実践者。大好きな言葉の仕事によって、今SDGsに取り組む皆様をご紹介 できることは、大きな喜びです。